Comprehending the Secret Parts and Repair Strategies for Product Packaging Equipment Upkeep
Reliable maintenance of product packaging devices pivots on a detailed understanding of their key parts, including the frame, drive system, and sealing mechanisms. Acknowledging usual upkeep issues, combined with the execution of preventative techniques and repairing techniques, can substantially enhance device integrity.
Trick Components of Packaging Makers
Packaging devices contain a number of crucial parts that work together to guarantee effective and efficient product packaging procedures. At the core of these makers is the structure, which gives architectural honesty and houses the numerous operating components. The drive system, often a combination of motors and gears, facilitates the movement of components, enabling accurate operation throughout the packaging cycle.
Another important component is the conveyor system, which transports items via different phases of the product packaging procedure. This is usually enhanced by sensing units and controls that keep an eye on the setting and speed of things, making certain synchronization and decreasing mistakes. The filling system is crucial for accurately giving the best quantity of item into packages, whether in fluid, powder, or solid kind.
Sealing mechanisms, consisting of warm sealers or glue applicators, play an important role in safeguarding bundles, preventing contamination and expanding life span. In addition, identifying systems are essential for giving needed product info, guaranteeing conformity with policies. Ultimately, the control panel, equipped with easy to use interfaces, enables drivers to handle equipment functions, display performance, and make adjustments as required, guaranteeing optimum productivity and performance in packaging operations.
Usual Upkeep Issues
Efficient procedure of product packaging devices counts greatly on regular maintenance to avoid usual issues that can interrupt manufacturing. Amongst these issues, mechanical wear and tear is common, specifically in elements like motors, conveyors, and seals, which can bring about unforeseen downtimes. Additionally, imbalance of components can lead to inefficient operation, causing products to be improperly packaged or damaged throughout the procedure.
Another common maintenance issue involves the accumulation of dust and debris, which can hinder the device's sensors and moving parts. packaging machine repair service. This not only affects performance yet can additionally posture safety and security threats. Furthermore, lubrication failures can lead to increased rubbing, causing getting too hot and ultimate element failure.
Electric troubles, usually originating from loosened connections or worn-out wiring, can disrupt equipment functions, leading to significant manufacturing hold-ups. Finally, software program problems because of out-of-date programs or improper arrangements can prevent the maker's operation, demanding instant intervention. Resolving these typical upkeep problems proactively is necessary for ensuring optimum efficiency and longevity of product packaging machinery.
Preventative Maintenance Approaches
Executing preventative maintenance approaches is important for sustaining the effectiveness and integrity of packaging equipments. These techniques incorporate a systematic technique to upkeep, focusing on the normal evaluation and maintenance of tools to preempt potential failings. By sticking to a scheduled maintenance program, drivers can identify deterioration on parts prior to they result in considerable failures.
Crucial element of a preventative upkeep strategy consist of regular evaluations, cleansing, component, and lubrication replacements based on producer suggestions. Making use of lists can simplify this process, guaranteeing that no vital jobs are forgotten. In addition, maintaining accurate records of maintenance tasks help in tracking the machine's performance with time, helping with notified decision-making relating to future maintenance requirements.
Training personnel on the significance of preventative maintenance enhances compliance and fosters a culture of proactive treatment. Applying an anticipating upkeep element, using data analytics and sensor technology, imp source can further optimize equipment efficiency by anticipating failures before they take place.
Troubleshooting Techniques
When encountered with malfunctions or ineffectiveness in packaging devices, employing organized troubleshooting methods is vital for identifying and settling problems swiftly. The very first step in effective troubleshooting is to develop a clear understanding of the maker's operational criteria and performance metrics. This entails evaluating the equipment's specs, as well as any type of error alerts or codes presented.
Next, drivers should carry out an aesthetic evaluation, examining for apparent indicators of wear, damages, or misalignment. This frequently consists of examining belts, sensors, click to read and equipments to pinpoint potential sources of breakdown. Gathering operational data, such as manufacturing prices and downtime logs, can also supply understandings right into repeating problems.
As soon as potential problems are identified, making use of a logical method to isolate the source is crucial. This may need screening specific parts or systems in a regulated manner. Engaging in discussions with operators who engage with the equipment consistently can yield valuable feedback about unusual actions or patterns.
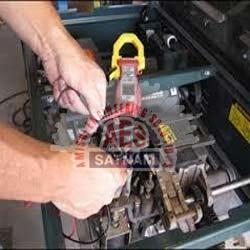
Fixing and Substitute Best Practices
A comprehensive understanding of repair work and replacement ideal methods is important for maintaining the long life and efficiency of product packaging makers. Frequently assessing the problem of device components permits timely treatment, avoiding even more considerable concerns that can cause costly downtimes.
When repair services are required, it is crucial to use OEM (Original Equipment Maker) components to make sure compatibility and efficiency. This not only maintains the integrity of the maker but likewise upholds guarantee arrangements. Additionally, it is a good idea to maintain a stock of essential spare components to promote quick substitutes and decrease operational interruptions.
For intricate repairs, engaging licensed technicians with specialized training in packaging equipment is advised. They have the competence to detect issues accurately and perform fixings efficiently. Additionally, documenting all repair service tasks and components replacements is essential for preserving a detailed upkeep background, which can assist in future troubleshooting.
Last but not least, carrying out an aggressive technique, consisting of routine assessments and anticipating maintenance methods, improves the dependability of packaging devices. By adhering to these best practices, businesses can ensure optimal machine efficiency, lower functional dangers, and prolong equipment lifespan.

Final Thought
In verdict, a thorough understanding of packaging maker parts and reliable upkeep strategies is important for ideal efficiency. By applying these techniques, companies can ensure the longevity and efficiency of packaging devices, eventually adding to enhanced functional efficiency and minimized prices (packaging machine repair service).
Reliable upkeep of product packaging makers pivots on a complete understanding of their vital parts, consisting of the framework, drive system, and securing systems.Efficient operation of packaging devices relies my company heavily on regular upkeep to protect against usual concerns that can interrupt production.Executing preventative maintenance strategies is essential for sustaining the performance and integrity of product packaging devices. Additionally, maintaining accurate documents of upkeep activities aids in tracking the equipment's efficiency over time, promoting educated decision-making relating to future maintenance needs.
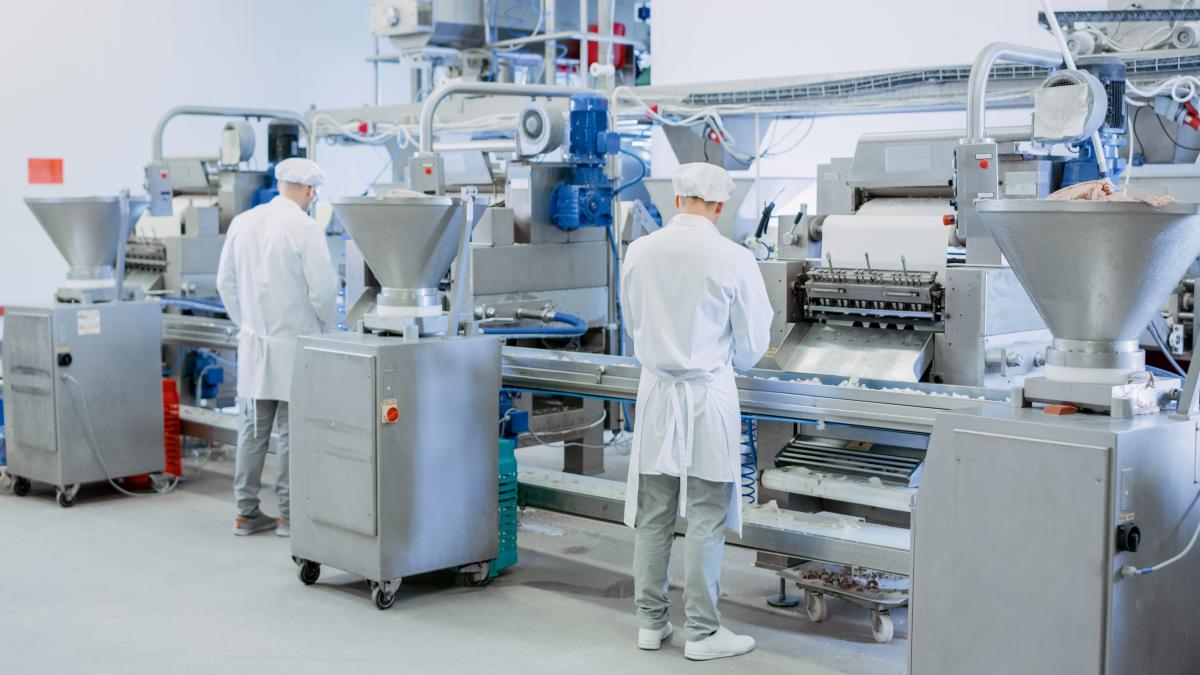
Comments on “Packaging Machine Repair Service: Avoid Delays and Enhance Performance”